
October 4, 2024 By Aharon Etengoff
Collected at: https://www.eeworldonline.com/which-connectors-drive-industry-4-0-automation/
Industry 4.0 automates (Figure 1) industrial, manufacturing, and logistics processes, leveraging artificial intelligence (AI) and machine learning (ML) to increase operational efficiency. Cables and connectors play a crucial role in Industry 4.0 networks, ensuring the seamless transmission of power, data, and signals.
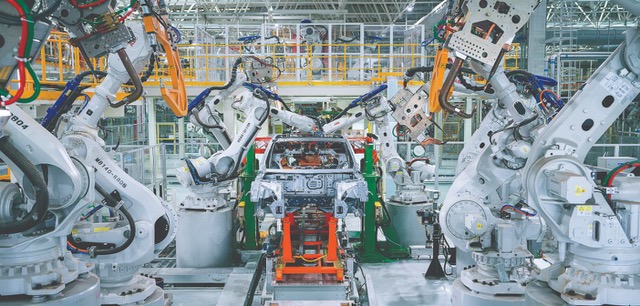
This article explains how Gigabit Ethernet forms the backbone of Industry 4.0 networks. It also outlines essential connector requirements like bandwidth, power, and signal integrity. Lastly, it reviews application-specific connectors and provides an overview of leading connector OEMs and distributors.
Gigabit Ethernet: the foundation of Industry 4.0
Industry 4.0 networks enable real-time communication between servers, data acquisition systems (DAQs), sensors, actuators, controllers, and Industrial IoT (IIoT) endpoints. Primarily Ethernet-based, these networks typically operate at 1 Gb/s, with some specialized deployments supporting advanced applications at 10 Gb/s or even 40 Gb/s. Using Power over Ethernet (PoE), Industry 4.0 networks deliver data and up to 90 watts of power to multiple edge devices over a single cable.
Many Industry 4.0 networks incorporate wireless technologies such as Wi-Fi 6/6E, Wi-Fi 7, and LTE or 5G. These wireless standards deliver fast and reliable connectivity for AI-driven cameras, sensors, and computer vision applications. They enable secure, low, and ultra-low latency communication for automated guided vehicles (AGVs), autonomous mobile robots (AMRs), and drones. Deployed indoors and outdoors, these networks support various use cases, such as factory automation, multi-building logistics facilities, and ports.
From bandwidth to modularity: understanding connector requirements
Industry 4.0 cables and their connectors (Figure 2) ensure reliable power, data, and signal transmission across interconnected components, devices, and systems. They also seamlessly link switches, access points (APs), radios, and small cells, maintaining stable and secure connections that support real-time communication and automation over short and extended distances.

To maintain signal integrity and operational efficiency, Industry 4.0 connectors must meet the specific technical requirements of their target applications, including:
- Bandwidth: most Industry 4.0 Gigabit Ethernet connectors support speeds of up to 10 Gb/s — crucial for real-time communication and protocols like EtherCAT, PROFINET, and OPC UA. Higher data rates ranging from 40 Gb/s to 100 Gb/s are achievable with advanced Cat 8 Ethernet cables and compatible connectors.
- Power: connectors safely handle high voltage and current and minimize power losses. Contact resistance, conductor materials, and plating optimize power transmission capabilities while shielding protects nearby devices from radio frequency interference (RFI) and ensures electromagnetic compatibility (EMC).
- Signal integrity: high-speed Industry 4.0 connectors optimize transmission by minimizing insertion loss and crosstalk. Robust shielding reduces RF interference and EMI, maintaining signal integrity near motors and power supplies, while integrated EMC suppression further mitigates interference.
- Durability: Industry 4.0 connectors operate reliably in harsh conditions, withstanding extreme temperatures, moisture, corrosive contaminants, and vibrations. Certain connectors in testing equipment, robotics, and industrial automation systems must withstand frequent connections and disconnections. IP-rated connectors, such as IP69K, secure cable retention and have a wide temperature tolerance (from -40°C to 125°C or higher), ensuring reliable performance in foundries, chemical processing plants, and material handling facilities.
- Termination: crimp, solder, or insulation displacement (IDC) termination types are generally selected to match application-specific requirements. In Industry 4.0 optical networks, connectors must accommodate secure fiber splicing, reliable termination, and precise alignment.
- Size and form factor: compact connectors with internal locking mechanisms or hybrid designs enable the integration of additional components in robotics, automated assembly lines, and sensor networks. Larger and medium-sized connectors support applications requiring higher power or data throughput.
- Standards compliance: Industry 4.0 connectors comply with numerous industry standards, such as the International Organization for Standardization (ISO), International Electrotechnical Commission (IEC), American National Standards Institute (ANSI), Telecommunications Industry Association (TIA), and Institute of Electrical and Electronics Engineers (IEEE). Many also support EtherCAT, CANbus, and PROFINET communication protocols.
Selecting connectors for Industry 4.0 networks
Selecting the most appropriate cables and connectors for high-speed Industry 4.0 networks ensures reliable communication and data and power transfers. Each connector type offers specialized features to meet specific application and environmental requirements.
Ethernet RJ45 connectors are widely deployed in manufacturing, industrial, and logistics. They link various devices and systems, such as programmable logic controllers (PLCs), human-machine interfaces (HMIs), DAQs, industrial computers, switches, APs, and edge devices like cameras and sensors. PoE versions eliminate separate power feeds while supporting speeds ranging from 100 Mb/s to 10 Gb/s. Recent advancements, such as Single-Pair Ethernet (SPE), transmit Ethernet over two twisted wires, reducing weight and copper costs.
Often deployed in harsher environments, either in place of or in parallel with RJ45s, circular M12 connectors feature a 12 mm locking thread specifically designed for industrial conditions. Available in multiple versions (3 to 12 poles), they provide reliable power, data, and signal transmission while resisting dust, water, and vibration. Notably, M12 connectors are coded to indicate their target applications.
With an 8 mm locking thread, Nano M8 connectors are smaller and more lightweight than M12 types, making them ideal for space-constrained applications, including sensor and actuator connections in factory networks. High-current power connectors efficiently deliver energy to machinery and robotic systems in rectangular or high-voltage circular form factors.
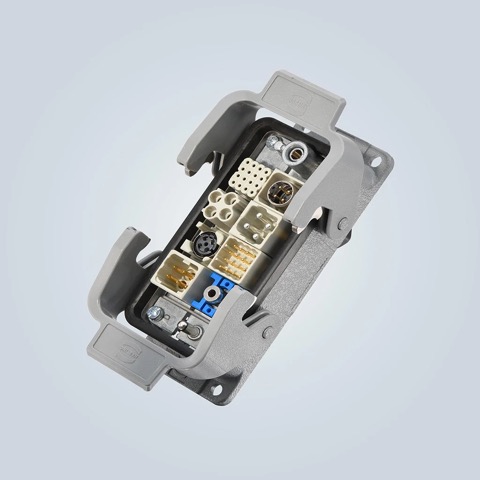
Additional Industry 4.0 connectors include:
- Fiber optic: fiber optic connectors facilitate high data transfer rates and offer near-complete immunity to EMI and RF interference, helping systems achieve electromagnetic compatibility (EMC). They span LC, SC, ST, and MPT/MPO types.
- Backplane: supporting high-speed communication between electronic modules or subsystems, backplane connectors link printed circuit boards (PCBs) to rack-based assemblies. Common backplane connectors in factory automation include DIN 41612, VME, CompactPCI, and PC/104.
- Electrical: high-current and high-voltage rectangular or circular connectors provide stable and safe power for Industry 4.0 applications and meet the demanding power requirements of automated systems.
- Fieldbus: Fieldbus connectors support communication protocols like PROFIBUS, CANbus, and EtherCAT, enabling synchronized automation across connected devices.
- Industrial USB: Featuring IP67-rated sealing, advanced EMI/RFI shielding, and resistance to harsh environments, robust industrial USB connectors are commonly used in DAQs, machine vision, and automation control applications.
- Slip ring: supporting multi-axis robots, turbines, and machine tools, slip ring connectors reliably transfer power, signals, and even liquids or gases between fixed and rotating Industry 4.0 components.
- Modular connectors offer flexible customization for power, signal, and data. M (Figure 3) combines multiple connection points into a single housing.
Leading suppliers of Industry 4.0 connectors
Many OEMs and distributors offer an expansive portfolio of Industry 4.0 connectors. For example, leading suppliers such as Mouser Electronics and Digi-Key maintain extensive connector catalogs to support manufacturing, industrial automation, and logistics. Popular connectors, including TE Connectivity’s RJ45 connectors, Phoenix Contact’s M12 connectors, and Harting’s modular connectors, are available for a wide range of automated Industry 4.0 applications.
Summary
Specially designed Industry 4.0 cables and connectors ensure the safe and reliable transmission of power, data, and signals. Network architects and system designers select connectors based on application-specific requirements like bandwidth, power, signal integrity, and termination.
Related EE World content
Four Types of Connectors for Robots and Drones
Rotary Slip Ring Connectors — What Are They Used For?
Connector and Terminal Products for Gas and Battery Powered Equipment
How Does Multidrop SPE Work?
How Does OPC UA PubSub Data Support Connector Digital Twins?
References
What is Industry 4.0?, IBM
Choosing the Right Connectors for High-Speed Factory Automation Networks, ConnectorSupplier
Why Connectors are the Enabler of Industry 4.0, ConnectorSupplier
Five Key Trends in Industrial Connectivity, ASME
Innovative Connector Solutions for Industry 4.0 and Sustainable Production, HRS
3 Connection Trends in Industry 4.0, Radiall
Leave a Reply