
JULY 15, 2024 by National Research Council of Science and Technology
Collected at: https://techxplore.com/news/2024-07-electrode-fabrication-electrolysis.html
A research team led by Dr. Sung Mook Choi of the Korea Institute of Materials Science has developed a one-step electrode fabrication process for the first time in South Korea. The research is published in the journal Applied Energy.
This process produces electrodes, a key component of anion exchange membrane water electrolysis, directly from raw materials to a mass-producible level. The team successfully applied this process to a commercial-scale stack of anion exchange membrane water electrolyzer.
This technology utilizes a one-step hot-pressing process that converts cobalt hydroxide into a cobalt oxide catalyst while simultaneously forming a highly uniform catalyst layer. This method replaces the complex steps of the existing process (hydroxide-oxide-crushing-dispersion-coating-drying) with a single coating step.
This achievement simplifies the process by 60% compared to the traditional method and enables the creation of a uniform catalyst layer. Additionally, it was confirmed that the efficiency of hydrogen production and the durability during continuous operation were significantly improved.
To optimize the one-step electrode fabrication process, the research team successfully fabricated a catalyst layer composed of uniform oxide particles, each 10 nanometers in size, by carefully controlling the cobalt (Co) hydroxide slurry conditions, as well as the temperature and pressure, which are key factors in the hot-pressing process.
Furthermore, the developed electrode was used to fabricate a membrane electrode assembly (MEA) incorporating an anion exchange membrane and a hydrogen evolution catalyst. Its stability and performance were confirmed in a commercial-scale water electrolysis cell.
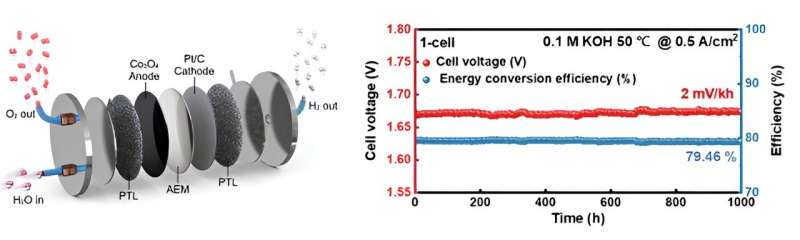
By applying the developed electrode to an anion exchange membrane water electrolysis system, the team demonstrated the possibility of achieving stable anion exchange membrane water electrolysis with high hydrogen generation efficiency (approximately 80% based on low specific calorific value) and a low degradation rate (2 millivolts per kilowatt hour for 1,000 hours of continuous operation).
Green hydrogen production from water electrolysis is expected to reach 11 million tons and 69 gigawatts of capacity by 2030. In Korea, efforts are underway to develop technology for demonstrating a megawatt-level anion exchange membrane water electrolysis system by 2024, with the aim of commercializing such a system by 2030.
Currently, the domestic level of anion exchange membrane water electrolysis technology is approximately 70-80% of world-class standards. This necessitates significant investment in related fields and an urgent need to secure core original technology and localize the technology.
Through the development of this technology, it is expected that by securing the source technology for the electrode manufacturing process that can be mass-produced, it will be possible to secure a global edge in related technologies, localize water electrolysis technology, and create and dominate overseas water electrolysis markets.
Dr. Sung Mook Choi, a principal researcher, stated, “By developing a one-step hot pressing electrode fabrication process with high process reliability, we have addressed one of the key challenges related to the commercialization of anion exchange membrane water electrolysis.
“If this technology is applied, we anticipate that mass production of anion exchange membrane water electrolysis will be possible, significantly reducing unit costs.”
More information: Shin-Woo Myeong et al, Highly durable and efficient anion exchange membrane water electrolyzer using one-step fabrication of the integrated electrode by the hot-press process, Applied Energy (2024). DOI: 10.1016/j.apenergy.2024.123650
Leave a Reply