JULY 25, 2022 by Ingrid Fadelli, Tech Xplore
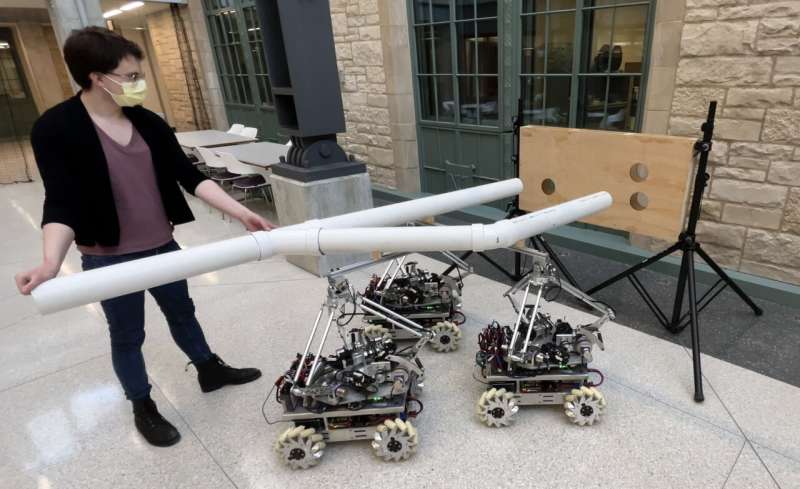
Teams of mobile robots could be highly effective in helping humans to complete straining manual tasks, such as manufacturing processes or the transportation of heavy objects. In recent years, some of these robots have already been tested and introduced in real-world settings, attaining very promising results.
Researchers at Northwestern University’s Center for Robotics and Biosystems have recently developed new collaborative mobile robots, dubbed Omnid Mocobots. These robots, introduced in a paper pre-published on arXiv, are designed to cooperate with each other and with humans to safely pick up, handle, and transport delicate and flexible payloads.
“The Center for Robotics and Biosystems has a long history building robots that collaborate physically with humans,” Matthew Elwin, one of the researchers who carried out the study, told TechXplore. “In fact, the term ‘cobots’ was coined here. The inspiration for the current work was manufacturing, warehouse, and construction tasks involving manipulating large, articulated, or flexible objects, where it is helpful to have several robots supporting the object.”
The collaboration between several mobile robots and human users can have several key advantages. Most notably, it merges the robots’ strength and precision with the adaptability and situational awareness of human users.
The Omnid Mocobot, the new robotic system introduced by Elwin and his colleagues, consists of a mobile base and a robotic arm. The robot has three important features that set it apart from other robots, making it particularly well-suited for manipulating objects in close collaboration with other humans and Omnid Mocobots.
“Firstly, the robot arms have built-in mechanical compliance,” Elwin explained. “This ‘softness’ means that the robots are safer for human interaction and are less likely to damage the object compared to typical robot arms. Second, the robot arms are designed to precisely control forces at their grippers, unlike most industrial robot arms. Third, the control laws governing the mobile base and manipulator are designed to allow teams of Omnids to cooperatively render a large object weightless to the human collaborator.”
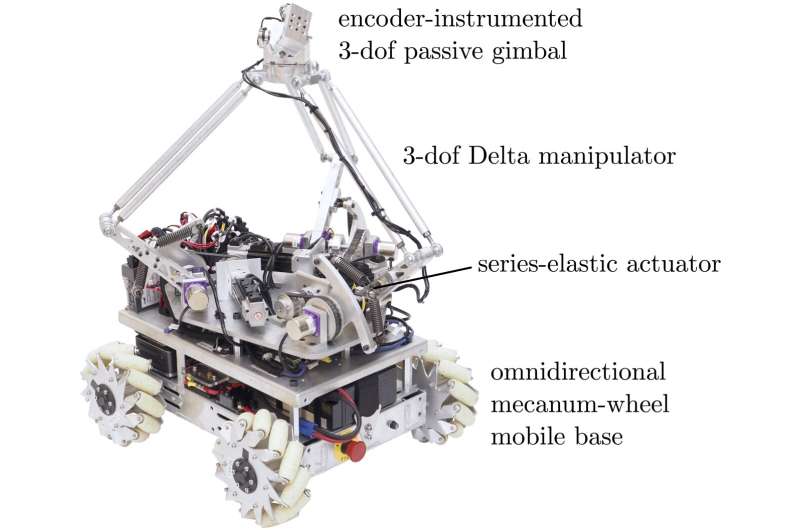
In their paper, the researchers outline several important considerations for the design and deployment of Omnid Mocobot teams. In addition, they share the results of several initial tests carried out in real-world settings.
In their initial tests, Elwin and his colleagues evaluated their robots’ performance as they collaborated with humans and other robots on tasks that involved the manipulation of large payloads. They found that when collaborating with three of their robots, a single human user was able to transport and precisely assemble a 15 kg pipe into a fixture, using a single hand.
Collaborative manipulation with the Mocobots is intuitive for the human user, so the human requires no training. The Omnids also do not have to be reprogrammed for tasks with different types of payloads.
“In the future, we envision larger teams of even more powerful Mocobots allowing one or a small number of humans to assemble large structures, such as a blade on a wind turbine or a solar panel on Mars’ habitat,” Elwin said. “The human would summon robots to grasp the object, and then the human would guide the assembly while the robots provide nearly all the required force.”
The new robots created by Elwin and his colleagues could soon be used to complete many collaborative manipulation tasks involving a human. The robots are currently incapable of autonomously manipulating objects using either preprogrammed controllers or strategies learned by observing their human collaborators, so this will be a goal for future research.
The researchers would now also like to test the robot’s ability to autonomously transport and assemble different objects, including fragile, articulated and flexible payloads. This would allow them to gain a better idea of the settings in which the robots could be deployed.
“In our next work, we also plan to incorporate more complex objectives, such as allowing humans to move the object while ensuring that the object does not move into restricted areas or experience forces that could break it,” Elwin added. “In addition, we will give the Omnids the capability to learn the kinematic and inertial properties of the payload and use this information for more dexterous manipulation.”
More information: Matthew L. Elwin, Billie Strong, Randy A. Freeman, Kevin M. Lynch, Human-multirobot collaborative mobile manipulation: the Omnid Mocobots. arXiv:2206.14293v1 [cs.RO], arxiv.org/abs/2206.14293#
Leave a Reply