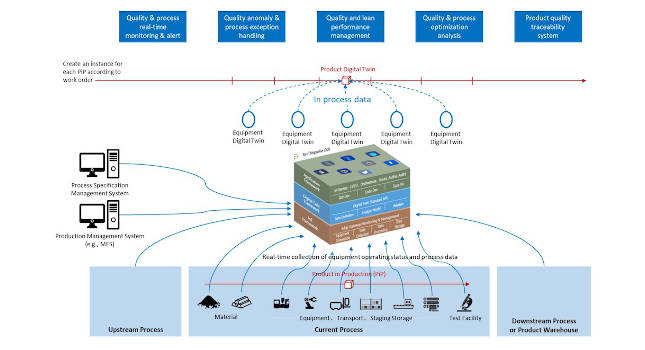
BY INDUSTRIAL INTERNET CONSORTIUM (IIC) JULY 28, 2021
Collected at: https://www.controleng.com/articles/optimizing-manufacturing-processing-and-quality-management-with-digital-twins-iiot/?oly_enc_id=9241B2802712G4S
An examination of the concepts and practices on the design, implementation and some preliminary outcomes based on a real-world use case in a production process control and quality management application in the steel industry, guided by Lean management and Six Sigma concepts and best practices.
The drive chain in the Industrial Internet of Things (IIoT) involves three key elements of data, analytics and applications[1]: data is collected from production environments including equipment, products and processes enabled by IoT, data analytics is facilitated by advanced analytics including machine learning, and smart industrial applications are driven by data and analytics to provide a closed feedback loop to support optimal business decisions, production processes and equipment states. Digital twin technologies[2] that systematically organize and synchronize data from the equipment, enable streaming data analytics, hence provide a dynamic representation of the production environment in the digital space. They further enhance the capability of smart industrial applications [3].
IIoT and digital twin in production environment. Courtesy: Industrial Internet Consortium (IIC)
The production process control and quality management application brings Industrial Internet, digital twin (including equipment and product digital twins), streaming and batch data analytics, machine learning, fused with Lean management and Six Sigma concepts and best practice into manufacturing process and quality management. By integrating and analyzing data from the equipment and other manufacturing IT systems, the system enables the correlation and monitoring of process design specification and actual process data, and quality data in near real time
- To identify and resolve production problems,
- Identify potential improvements in current and new manufacturing processes through the quality-process feedback loop, and
- To provide track and trace capability on product quality on individual products through the implementation of product digital twin.

The system helps the manufacturing operator to ensure product quality and reduce production cost.
The concepts and practice of the Industrial Internet have been widely applied in various industries. The implementations of digital twins are starting to pick up in industries as well. At this moment, however, these implementations are disproportionally in the area of equipment maintenance in the large domain of asset management with novel features such as predictive maintenance supported by advanced analytics. There are few and far between real world use cases penetrating in the production processes covering broader application domains such as production process, quality, energy, equipment and operation safety management, each of which presents a deep and rich field where IIoT and digital twin technologies can offer great potential benefits and characteristics include:
In a previous volume of Journal of Innovation published by the Industrial Internet Consortium, part of the authors of this article co-authored an article reporting a real-world use case of the Industrial Internet and digital twin in energy management in the steel industry[4]. In the same vein, the application of IIoT and digital twin technologies in production process and quality management in steel production processes with the following characteristics:
- Integrate process design data, quality specification data, equipment operational real time data, quality measurement data into a holistic end-to-end closed-loop system, enabling comprehensive online monitoring and analytics of production process and supporting product quality traceability.
- Combine digital twin and Industrial Internet technology seamlessly into a holistic platform to support such an application.
- Enable digital twin for both equipment and product alike, dynamically bind product digital twins with equipment digital twins to enabling product process and quality online tracking, monitoring and traceability.
- Combine online data and analytic technologies with Lean management and Six Sigma concepts and best practice for production process and quality management, creating a digital Lean capability.
Problem domain
The usage scenario involves production processes in steelmaking, an important continuous process heavy industry. More specifically, it involves the later processes such as forging and heat treatments in special steel production after raw molten steel has been casted into slabs, blooms or billets. However, the basic approach and technologies used in this scenario can be extended and applied to other similar processes in steelmaking or other similar industries as well.
Complexity in steelmaking processes
Steelmaking involves many long and complex production processes. It takes in iron ore, coal, limestone and recycle steel as raw materials and produces products that include common steel and a phalanx of special steel used for making parts for various of machines. In between, it goes through many major processes, such as coke oven, blast furnace or direct reduction furnace to produce iron, basic oxygen furnace or electric arc furnace to produce molten steel, continuous casting to produce slabs, blooms and billets as intermediate products in the primary production processes. Then in the secondary production processes, the intermediate products are reheated, forged or pressed into various forms, such as pipes, sheets, bars, rods, and other structural shapes, which may be further heat treated, surface-coated and finished before being released as products.
Steelmaking primary production processes. Courtesy: Industrial Internet Consortium (IIC)
Further complexity in steelmaking arises from each of the major production processes may consist many subprocesses, each of which may be supported by various production lines that employ many large and sophisticated pieces of equipment with complex upstream and downstream supply chain relationship. In the primary processes, steelmaking is largely a continuous process.
Moreover, production process parameters in the upstream processes have strong influence over the downstream processes. The production process of high-end special steel is even more complicated involving more processes and sub-processes. Another rather unique aspect in steelmaking is its products in process subject not only to mechanical but also chemical changes, making its quality monitoring and tacking more challenging. The making of special steel tends to consist of small batches of large varieties of products. At the same time, because special steels are used in important equipment of various industries with higher reliability and safety requirements, and in turn the requirements for quality are more demanding and refined. The need for traceability of product quality in its full production lifecycle is also stronger.
Steelmaking secondary production processes. Courtesy: Industrial Internet Consortium (IIC)
Achievement and challenges in digital systems in the steel industry
For the past few decades, steelmaking, like many other continuous process-heavy industries, has been automated at the equipment level (ISA-95 level 1 and 2). Programmable logic controllers (PLCs) and supervisory control and data acquisition (SCADA) systems are used to control and monitor the production processes. The steel industry also has invested in establishing various IT application systems managing one or other aspects of productions such as production planning and execution with manufacturing execution systems (MES), production process control management system, quality management system (QMS), equipment management system, all belonging to at the ISA-95 level 3. The steel industry is operating based on these systems that have significantly contributed to the increase of productivity, improvement in product quality and reduction of production cost.
However, a number of major technical challenges remain:
- At ISA-95 Level 1 and 2: Many PLCs often remain unconnected to higher level systems, so it is impossible to collect data from them. For PLCs that have been connected to SCADA systems, it is often that the SCADA systems remain isolated so the data that have been collected or alerts that have been generated can only be viewed locally using associated HMIs. Data and alerts in one SCADA system cannot be readily used to correlate or otherwise analyze with data from other systems. Analytics, if any, often requires manual work that are technically involved, time-consuming and unreliable, and remain to be ad hoc, incomplete, inconsistent, usually carried out too late to be useful.
- At ISA-95 Level 3: The existing application systems tend to be built over different periods of time, often sponsored by different departments with a strong focus on solving specific domain problems such as equipment maintenance without enough thoughts given to forming holistic view and considering the interaction of different aspects of the overall operations. Worse still, these systems were contracted out to third-party software integrators who built these systems independently, often with completely different designs and data models supported by different technology stacks with few functions exposed as APIs. Consequently, these systems operate on their own and has little integration with other systems, forming stacks of independent application silos and unreachable and reusable data islands. Furthermore, there are domain areas that are not yet covered by modern software application systems; thus, its operations still require manual data entry and tracking.
- Between ISA-95 Levels: Few Level 3 application systems have comprehensive connectivity to the Level 1 and Level 2 systems making it difficult to obtain near real time data for advanced analytics in and across the application systems.
At present, the production operation management of steelmaking have been established on the basis of automation systems and IT application systems as briefly described above. However, there exist connectivity and integration barriers in the current systems preventing further improvement in operation efficiency from realization. These barriers in a major part are resulted from the technical challenges outlined above, between the production operation management application systems and the equipment automation control systems (PLCs and SCADAs), and among the application systems themselves.
The first type of barriers exists between the IT application systems and the automation systems because the PLCs and SCADAs are not nearly sufficiently connected to the application systems, causing many application systems separated from, or only weakly linked to, the physical reality of the production environment where equipment is in operation and products are being processed. The result is that the data in the underlying automation systems has not been fully collected and utilized, making it almost impossible to gain transparency over the status of production processes leaving alone the possibility for data and analytics-driven management of the operations.
The second type of barriers exists among the applications systems in various applications domains and in various production processes and lines,. This is largely the consequence of history in that the technologies of the past were not conducive to enable interworking of various applications in the very complex environments such as those in steelmaking. This leads to the situation in which application systems in different domains, or in the same domain but in different upstream and downstream processes, have not achieved the level of information integration and exchange that are needed, so it is very difficult to support cross-process and cross-domain holistic and dynamic data- and analytics-driven operation management.
Steelmaking process control and quality management challenges
The challenges and potential opportunity for improvements in the smaller scope of the two closely linked application domains: production process and product quality management, are similar.
- It is common practice that the existing process management applications are mainly responsible for information management of product specification, production process and quality design. Too often these systems are not connected to the production management systems, and therefore the transmission of detailed process control specification for specific products still relies on conventional electronic documents exchange to reach the on-site production management systems and thus requires manual configuration of the processes.
- Additionally, most of the on-site operation process data and quality data cannot be automatically collected but rather to rely on manual reports to track, trace, and archive. As result, it is difficult to discover quality issues soon enough so they can be addressed in time for corrective actions to advert or minimize the impact. Therefore, problem root cause analysis and solving if any are often after the fact.
- Quality analysis is still a manual exercise on static historical data using conventional SPC-like toolsets that are not connected to the production environment.
- Production process control specification and on-site operation data and quality outcome are not easily correlated to provide guidance on product and process control design.
- Product full lifecycle quality traceability is hard to achieve.
- Moreover, the process management put too much manual operational and recording workload on workers that are not efficient and prone to error.
The main quality attributes of steel products include structure performance determined by micro-structure of the material, surface quality and geometric dimensions, which mainly depend on the composition of the material and the processing technologies involving chemical reactions, thermal dynamic and mechanical processing during the production processes. Therefore, it is necessary to obtain data and information related to the three main categories of quality attributes and process control design with respect to the customer’s requirements.
The quality pass rate of steel products, especially high-end special steel products, is often low. The main cause for this is the relatively weakness in process control that leads to large fluctuations in the processes that inadvertently affect the quality of the final products. There are many challenges contributing to the weak process control, such as the difficulty in maintaining stability of process control parameters, in detecting interference of uncontrollable factors, and in practice, due to the lack of means, there are many influential process parameters are not only uncontrolled but often not yet visible.
Additionally, many product quality issues are related to equipment status and operation methods. Therefore, in order to obtain quality products, standards need to be formulated and quantified for ingredients, processes, equipment, and operation methods, and equally crucial, there need to be real-time measurement and monitoring the actual process to ensure these standards are met, and any exceptions are detected promptly so they can be corrected in time.
Furthermore, the quality of steel product is affected by many coupling factors. Constrained by practical conditions, it is impossible to control every factor that may affect quality. To improve product quality, the key is then to identify the key factors and place strong emphasis on controlling them. However, the cause-and-effect relationship of various factors are often complex and coupled with each other, thus brings great challenge in identifying what the key factors are without in-depth analytics. On the other hand, the analytics for this and other similar purposes depends on large amount of quality data that contain the correlations between what seem to be randomly occurring defects to process control specifications and actual process data, equipment status and operational methods that may cause the defects.
These obviously cannot be accomplished with the conventional approach of relying heavily on spotted manual inspection and recording, and by counting on the independent and isolated automation systems and application systems that cannot share and align data. A totally new approach supported by a new set of technologies is required to address these challenges to achieve total quality control in the production environment. At this time, the IIoT and digital twin technologies are the right choice for addressing these challenges, as demonstrated by our practice.
Industrial internet platform with embedded digital twin framework as solution
A successful solution was found using an industrial Internet platform embedded with a digital twin framework to break through the barriers at different architecture levels and among different domain application systems as described above. The final solution system:
- Carries out collection of process control and quality data, enables near real-time data analytic, establishes a new data- and analytics-driven production process and product quality management application.
- Performs online dynamic comparative analysis on actual process data in reference to process design specification, carries out dynamic process quality monitoring and quality traceability of products, discovers process exceptions and quality anomalies and enables quality issues resolution in time.
- On this basis, moreover, through statistical analysis of data, enables process verifications and improvements.
It helps production operators to achieve the goal of avoiding defective products, improving product quality, and reducing production costs.
Although the technical approach, technologies and solution are applicable in the wider use scenarios in the steelmaking processes, the project reported here initially focus one of the steelmaking processes, namely, the forging process to get started, verify and improve the solution before expanding into other processes [6].
Lean Six Sigma design process
After a development contract was completed with the customer during which a preliminary use scenario research was carried on site, a comprehensive on-site discovery-research was carried out by a team with expertise in various domains, which mainly include:
- Industrial domain experts with deep insights about steelmaking processes who help to understand the production operation processes and are capable of evaluating the business needs of the customers from which to derive business requirements.
- Industrial software application analysts who work with industrial domain experts to translate business requirements into software requirements and assist the design of the software solution.
- Industrial data analytic engineers who are experienced with data modeling techniques to understand the data analytic requirements and map them into input data and modeling requirements.
- Industrial control/automation engineers who are responsible for gathering information about the deployment structure and configuration of the industrial equipment and other systems involved in the project, evaluating the connectivity and data collection requirements and design the IoT portion of the software solution.
Among the multi-dimensional on-site research, the most critical work is the evaluation of customer requirements in establishing this new production process and product quality management application which is to become a major tool to be used by production operators and managers alike in their respective daily work. The Lean management and Six Sigma concepts and best practice, having long been proven to be effective in in production operation management, are used as guiding principles to evaluate the production process and product quality management practice in order to come up with the business requirements, which partly requiring changes in the operation processes and organization, and partly to be implemented by the software solution, in a way to solidify and augment the operational management methodology and best practice in software.
The Lean management approach relies on three key ideas [7]:
- Identify the value and value stream in an operation flow or process to drive value delivery
- Eliminate waste (things that do not bring value to the end product)
- Continuous improvement.
The Six Sigma [8] approach aims to management processes that can be defined, measured, analyzed, improved, and controlled (DMAIC) using a set of advanced statistical and project management toolset with a goal of keeping tolerance of fluctuation under ±6σ (standard deviation of the requirement).
Examples of process control parameter real time monitoring with built-in statistical analysis and alerts. Courtesy: Industrial Internet Consortium (IIC)
Lean management is keen on driving out waste, promotes standardization in workflows and procedures, and continuing improvement, whereas Six Sigma focuses on reducing process variation and enhancing process control. These two methodologies in management overlap and otherwise complement each other with diminishing distinction.
Based on the Lean management and Six Sigma principles, the on-site discovery-research and evaluation of customer requirements focus on:
- Standardization of operation: Standardize operation workflows and procedures that deliver the values – quality products, against a set of constraints and uncertainties, and seek to maintain the operation standard with the software as much as possible.
- Waste reduction: Reduce the occurrence of defects in the products and the amount of re-work needed to address quality issues. The key approach include:
- To exercise the best data-driven control over the production system to maintain stability of the processes avoiding unwanted or unnecessary fluctuations;
- To discover process exceptions and quality anomalies in near real time and identify their root causes so they can be addressed in time to avoid downstream wastes;
- Continuous improvements: To provide online visibility to the quality performance including using conventional Statistical Process Control (SPC) methods, however, based on real-time data so quality performance issues can be identified and addressed by enabling:
- Per-operator/workgroup longitudinal quality performance comparative analysis;
- Cross-operator/workgroup lateral quality performance comparative analysis;
- Per-product type longitudinal quality performance comparative analysis;
- Cross-product type lateral quality performance comparative analysis;
- Product defect multivariant-correlation analysis, considering factors in product design specification, process specification, actual process data, work procedure details, and individual operator skill levels, etc., to identify principal factors that contribute to the occurrence of defects so measures can be taken across different areas to improve design, processes and procedures and operator skills.
Information flow of data and analytic-driven total quality management supported by real time process control. Courtesy: Industrial Internet Consortium (IIC)
Most of the capabilities described above can and must be designed into and implemented in the software application to cement the methodology and best practice so they are exercised in the production processes largely automatically. The foundation of realizing most of these capabilities is data collection across all equipment and other operational systems involved in the production processes. On this basis, the project use software to comprehensively digitize the operation processes and procedures, enforcing to a large degree standardized operation workflow. It then leverages advanced analytics to help to optimize the operation management.
The project leverages the power of data and analytics, and the capabilities of software to implement and enforce Lean management and Six Sigma principles, realizing a data- and analytic-driven digital Lean management and Six Sigma system for production process and product quality management.
Production environment configuration
The phase I of the project limits its scope to a special steel plant, part of a larger steelmaking process, that consists of multiple heat treatment and forging processes and production lines that include electric furnace production line, electroslag furnace production line, double vacuum production line and forging production line. The furnace equipment involved includes electric arc furnace, induction furnace, refining furnace, conventional electroslag furnace, gas-protected electroslag furnace, vacuum induction furnace, vacuum consumable furnace, etc. that come with different forms, such as trolley furnace, indoor furnace, ring furnace, etc. The configuration of the equipment is schematically illustrated in Figure 3‑4. Each furnace can perform heat treatment of multiple products in production (PiP) at the same time. However, each of the PiP may be treated according to different process control requirements.
Logical and information flows for quality exception handling to reduce wastes. Courtesy: Industrial Internet Consortium (IIC)
Each type of equipment deployed in a given process may be of different models with varying capability and capacity. All the equipment as a whole can be roughly considered as a node in matrix or a graph [9] in which each PiP moves through during the production process. Because special steel products have many varieties and are being made in small batches, with each product type needing to meet specific product specification and to be produced with specific process control parameters. Furthermore, multiple products are often being produced at the same time. Consequently, the production scheduling for each PiP is dynamic to maximizing equipment overall equipment effectiveness (OEE) and production capacity. Therefore, each of PiP, even of the product type, may take a specific and unique path in the equipment matrix during its lifecycle of production.
In order to achieve the design goal of the application, it is required keeping track not just the path of the PiP in its lifecycle of production, but also its own set of actual process data when it is being processed by each piece of equipment and its characteristics (such as its temperature) in the staging area between equipment.
A equipment and workflow process in special alloy steelmaking plant. Courtesy: Industrial Internet Consortium (IIC)
System design requirements
The Lean management and Six Sigma-oriented customer requirement evaluation presents a few key requirements on the system design:
- The need to realize full lifecycle tracking of product in production (PiP), including its movement in the production processes, its dynamic association with production equipment during the time when it is being processed and the corresponding actual process data, and for some situation, its conditions during transitional staging periods.
- The need to align each piece of PiP’s actual process data with its corresponding process specification parameters to ensure the actual process data are within the required design range;
- The need to automatically detect and provide alert on process exceptions and product anomalies, and in some cases to provide automatic or semi-automatic root cause analysis for the detected exceptions and anomalies.
- The need to connect to work order system to obtain work dispatch information; the need to connect to production process specification management system to obtain process specification for each PiP; the need to connect to product quality test system to gather and record test outcome associated with individual PiP.
- The need to provide online analytics based on the data collected to support online and batch quality performance and other analytics.
This is a use case that can clearly leverage the capabilities an IIoT platform with a digital twin framework can offer:
- IoT capability to connect to equipment and sensors to collect data;
- Comprehensive digital representation, namely, digital twins, of the production environment, most importantly, the equipment twins and the product twins to track their status and process data, and the dynamic relationship between PiPs with the equipment so actually process data can be collected and correlated with the PiPs;
- Analytic capability that can be digital twin-embedded to analyze data associated with equipment and PiPs
- Application DevOp environment for develop and running the application that implement the business logic and user interfaces.
IIoT platform and digital twin framework-based design
The system design is based on the Yo-i Thingswise Industrial Data OS (iDOS), an Industrial Internet Platform embedded with a digital twin framework, purposely designed, in reference to Industrial Internet Reference Architecture[10], for supporting digital transformation of industrial operational management.
Yo-i Thingswise iDOS platform functional architecture. Courtesy: Industrial Internet Consortium (IIC)
It is built on a core architecture that integrates cloud-native technology, Big Data, machine learning (ML) and micro-service technologies as its foundation on which a set of innovative key functional components are developed to provide a flexible to deploy, easy to use, self-contained end-to-end industrial platform-as-a-service (PaaS) stack. As an industrial PaaS platform, it provides:
- An IoT Framework to support connectivity to equipment and devices for data collection and system control. It offers the following features:
- Equipment connectivity
- Data collection
- Data preprocessing
- Data storage
- IoT gateway remote management service.
- A digital twin framework to digitally represent production environment, manage equipment data, and integrate analytic models associated with the equipment.
- Digital twin design GUI
- Digital twin to IoT data mapping
- Digital twin analytic modeling
- Digital twin API.
- An application (DevOp) framework to enable GUI-based codeless and normal code-based application development, deployment and runtime management.
- Data visualization tool
- GUI-based application rapid development tool
- Multi-language code-based application development SDK
- Micro-service framework.
The full technical stack of the platform, as shown in Figure 3‑5, supports end-to-end streaming data processing and analysis, enabling near-realtime responses to events occurring in the industrial operational environment. It is designed to enable industrial enterprises to develop and run data and analytic-driven industrial smart application.
System architecture example. Courtesy: Industrial Internet Consortium (IIC)
Implementation key points
The overall system architecture based on the platform described above is illustrated in Figure 3‑6.
- Equipment connectivity and data collection, integration to other systems, such as process specification management system (to obtain product process specification) and production management system (to obtain work order information) are implemented with the IoT framework layer of the platform (including IoT/application integration gateways), through GUI-based codeless configuration. The connectivity to equipment involves various common industrial connectivity protocols that include MODBUS, OPC UA/DA, and a few proprietary protocols.
- Digital twin system representing all the relevant equipment and products are designed and configured. Within the GUI-based digital twin designer, digital twin classes (see Figure 3‑7) are created where equipment state variables and equipment process control parameters are defined as digital twin data fields, along with their metadata. Then based on the number of instances of each equipment type, the digital twin classes are instantiated to represent the actual equipment instances. The data collected from the IoT framework is mapped to data fields in each of the digital twin instances using the GUI-based or configuration file-based batch import toolset provided by the platform.
- Data analytic models are at the heart of this solution. There are various analytic models tracking the process parameters to ensure they each falls within the standard range on the basis of each individual PiPs. Furthermore, because of the complexity of the production processes that involve many uncontrollable process parameters. It is not always possible to rely on single parameter range checking to determine if the process is running optimally or if certain combinations of otherwise normal ranged parameters would be conducive to product defects. The relationships among these parameters are often nonlinear, strongly coupled and some with direct or indirect feedbacks among themselves and making them difficult to assess the cause-effect for product defect or other considerations. It is crucial to gather as much as possible data from the production environment for modeling, including leaving sufficient data for model validation.
- The applications, support the following business functions that map to the requirements described above:
- Quality and process real-time monitoring and alerting
- Quality anomaly and process exception handling
- Quality performance Lean management
- Quality and process optimization analysis
- Product quality traceability system.
Digital twin class (equipment type) design GUI. Courtesy: Industrial Internet Consortium (IIC)
The application is designed with a role-based user interaction model to improve user experience and enhance application security. Users of the application is divided into different roles based on their job functions and area of operations (in different processes). Each user can assume one or more roles based on the production organization details. When a user logs in, the application presents pages corresponding to the specific roles the user assumes. The application relies on the platform user authentication and fine-grain role-based authorization framework without the need to develop customer codes for the set of functions.
By leveraging the platform capability, a large portion of development work, including IoT connectivity and data collection, and digital twin design, are completed using GUI-based design and configuration toolset without the need of any coding. As result, development workload is great reduced and development cycle are substantially shortened.
For the business functions in the upper layer, though requiring code development, its scope is greatly reduced to just focus on business functions with user interaction through the UIs. In dealing with equipment and products (physical entities), the application interacts with the corresponding digital twins through their APIs, avoiding the need to deal with complex custom databases or directly with the equipment or product, it greatly simplifies the development of the application.
A screenshot of the overall process status view. Courtesy: Industrial Internet Consortium (IIC)
Since the application interaction with the physical entities is abstracted out by the digital twin layer, the application to a large degree is isolated from the physical environment in such a way that if the equipment changes, it is only needed to modify the underlying digital twin configuration without the need to change the application codes. This makes the application much more portable from one physical environment to another, for example, to the same process in another steel plant.
The end-to-end application also benefits from the security, scalability and reliability in part provided by the cloud-native distributed architecture in the platform, freeing the application developers from concerns about system security, performance and reliability in their development.
Product digital twin
The concept of equipment digital twin is well understood. However, the concept of product digital twin in production is less reported. The equipment and product digital twins play important role in production process and product quality management as reported in this article.
For material product (in contract to machine or electronic device product) such a steel, the product in production subjects to various transformations, including in physical form (solid and liquid), physical properties, shape, surface properties, and micro-structure through chemical reactions, thermal and mechanical processes. Many of the transformation outcomes are not directly measurable in real time, either not easily measurable by simple sensors, or the sensors could be easily destroyed subjected to the harsh processing environment. Some properties require lab tests that will take hours or days to complete.
Except for a few relatively simple tests, such as hardness or surface properties, the quality of steel product relies heavily on ensuring the accuracy and stability of production process control. The process control data are properties of the production equipment and are relatively easy to collect from the equipment control systems. In order ensure the product quality in every processing phase or step, it is important to track the product in production (PiP) in association with the production equipment.
In this project, PiP tracking is done with product digital twin. From information in the work orders, the system automatically creates product digital twin for each PiP. The initial product digital twin model includes information such as its ID, product type, process specification, etc. As the PiP moves through different stages in its production process, a dynamic association is made with the equipment that is processing the PiP from which key attributes such as start and end processing time and other attributes. Any relevant actual process data from the equipment is also automatically entered into the product digital twin, and dynamically analyzed in reference to its corresponding process specification at that processing stage. Any deviation from the process specification by the actual process data can be identified, recorded and reported. Similarly, any records of quality measurement and inspection will also be entered into the product digital twin as well. When the processing of a PiP is completed, the data of the full life cycle of the product in the production process is also fully recorded and ready to be queried and analysis in the corresponding product digital twin model.
To consider the product digital twin in a different angle, products are what manufacturers made to create value for its enterprise. As the product in process moving through the production processes, it represents the value flows of the production. By tracking the product in process via product digital twin through the production processes, it in fact is tracking the value flows of the manufacturing enterprise. By further considering the raw material costs, energy cost, defect cost, the OEE of the equipment, labor cost, and the market or order prices of the final products, etc., it is possible to compute and visualize in near real time the value that are being created throughout the production environment. This will help the manufacturer to better manage the production in identify and reduce or eliminate cost and maximize value creation by making informed decisions in what to make and how to make them.
Conclusion and learnings
By leveraging the built-in capability of Yo-i Thingswise iDOS platform, the complex project was completed from design to delivery and acceptance in about 3-4 months, less than half of the time it might need should the platform were not used. The production process and product quality management system were well received by the customer during the initial phase of trials.
There are a few points of learning from this project:
- IIoT, digital twin, industrial analytics are enabling technologies (not applications by themselves), most fitting for supporting a new generation data and analytics-driven industrial operation management applications.
- IoT, digital twin and industrial analytics technologies must be fused with proven management methodologies and best practice, such as Lean management and Six Sigma, to be truly effective to provide values to the industrial operation management settings. (In other words, IoT or analytics decoupled from operation management only provides limited value.)
- IIoT, digital twin and industrial analytics technologies have great potential in advancing the digitalization of industrial operation management, in domains beyond equipment maintenance to include production process and product quality management (as demonstrated in this article), energy management (as reported in our other article, see 4, and possibly production planning and execution as well.
- Both equipment and product digital twins are effective methodology and technology to track product quality as the product being processed and to build product quality traceability records. Product digital twins in fact can be used to represent the value flows in the manufacturing floor.
- IIoT platform with a digital twin framework has been proven to greatly simplify the implementation of industrial operation management solutions that is secure, scalable and reliable.
References
[1] Industrial Internet Reference Architecture. V1.9. Available: https://www.iiconsortium.org/IIRA.htm
[2] Digital Twins for Industrial Applications. Definition, Business Values, Design Aspects, Standards and Use Cases. An Industrial Internet Consortium, White Paper. Version 1.0 2020-02-18. Available: https://www.iiconsortium.org/pdf/IIC_Digital_Twins_Industrial_Apps_White_Paper_2020-02-18.pdf
[3] M. Bärring, B. Johansson, G. Shao, Digital Twin for Smart Manufacturing: The Practitioner’s Perspective, SME International Mechanical Engineering Congress and Exposition, Proceedings (IMECE), Nov, 2020.
[4] Shi-Wan Lin, Maxine Fu and Kebin Li, Digital Twin + Industrial Internet for Smart Manufacturing: A Case Study in the Steel Industry, Journal of Innovation, Industrial Internet Consortium, Nov. 2019.
[5] https://www.steel.org/steel-technology/steel-production/
[6] As of the writing of this article, the first phase of the project has been completed and customer acceptance has obtained. A related project in a different steelmaking process has been launched.
[7] https://kanbanize.com/lean-management/what-is-lean-management
[8] https://asq.org/quality-resources/six-sigma#:~:text=Six%20Sigma%20is%20a%20method,quality%20of%20products%20or%20services
[9] as a concept in computer science
[10] Industrial Internet Reference Architecture. V1.9. Available: https://www.iiconsortium.org/IIRA.htm